Humidity Freeze Test Chamber for Solar Panels
To determine the ability of the module to withstand the effects of high temperature and humidity followed by sub-zero temperatures. After the fabrication of a high power photovoltaic (PV) module, the most critical aspect is the duration for which the module can produce useful power. Reliability and lifetime of photo-voltaic (PV) modules are key factors to system performance and warranty and thus are extremely important as far as PV business is concerned. Outdoor field testing is an accurate method in estimating module lifetime. However, since PV modules commonly come with twenty five years of warranty, testing modules in field for that long period is not feasible. Thus, due to time constraints, many accelerating aging tests have been derived over the years for testing reliability of PV modules. The accelerated test protocols established by organizations like IEC and UL have been adopted worldwide as official tests to evaluate module quality and reliability standards.
To determine the ability of the module to withstand the effects of high temperature and humidity followed by sub-zero temperatures. After the fabrication of a high power photovoltaic (PV) module, the most critical aspect is the duration for which the module can produce useful power. Reliability and lifetime of photo-voltaic (PV) modules are key factors to system performance and warranty and thus are extremely important as far as PV business is concerned. Outdoor field testing is an accurate method in estimating module lifetime. However, since PV modules commonly come with twenty five years of warranty, testing modules in field for that long period is not feasible. Thus, due to time constraints, many accelerating aging tests have been derived over the years for testing reliability of PV modules. The accelerated test protocols established by organizations like IEC and UL have been adopted worldwide as official tests to evaluate module quality and reliability standards.
Humidity Freeze Test is performed according to IEC 61215. PV modules are subjected to cycling between temperatures 85°C with relative humidity 85 % and -40°C. PV modules are subjected to 10 complete cycles in the closed climatic chamber in accordance with the profile on the picture bellow. The purpose is to determine the ability of the module withstand against humidity penetration.
Got Technical Question!
Description | Specification | ||||
Workspace Dimensions - WxDxH | |||||
mm | 2040 | x | 2400 | x | 2400 |
In | 80 | x | 94 | x | 94 |
Volume | |||||
Ltr | 11750 | ||||
Cuft | 415 | ||||
Temperature Range | |||||
°C | -40 | To | 100 | ||
°F | -40 | To | 212 | ||
Ramp Rates | |||||
Cooling °C/min | 3.3 | ||||
Heating °C/min | 3.3 |
Ethernet
Ethernet capability to remotely monitor and control the chamber.
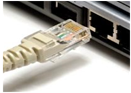
USB
USB Type-A host port to connect a keyboard or mouse or download CSV data via pen drive [max 2GB] USB Type-B data port for connection to PC for software upgrade and access memory card storage
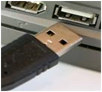
Web Server
Built-in web server allows remote view or control from any internet connected PC, tablet or smart phone
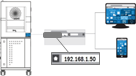
NI Lab view
The communication which used is MODBUS RTU protocol, which is an international standard for communication in process instrumentation and automation. Necessary changes to be made in the user’s software to communicate this in MODBUS RTU universal protocol. This feature can be used manual mode only.
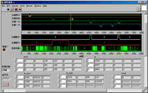
Hardware
Enhanced with modular controller integrating multi-zone PID control and data acquisition. SIMATIC programmable logic controller. Touch screen controller, PLC and other controller components are of a generic make with an OEM software. Free software upgrades up to one year.
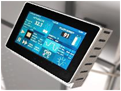
Memory
SD card of 2GB memory will store all the test program data and also the diagnostic data. This card is accessible by USB and Ethernet.
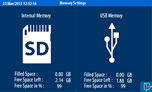
Digital Events
1 digital output for switching test specimen via potential free contacts, load max. 24 VDC, 5A
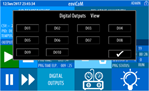
Programs
99 independent programs can be stored with name and number. Each of these programs have segments which can be looped to a previous segment and repeated up to 999 cycles, creating almost unlimited number of segments The chamber can be operated in manual mode, where the set point can directly be changed in the home screen The ramp rate can be set as a value in °C/min or ramp time Graphical representation of the temperature program The time is logged only when the set valve is within the band.
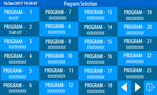
Trend Graph
Real time trend graph for temperature set value, temperature process value, humidity set value and humidity process value. Options of zoom in/out, pan and individual plot selection
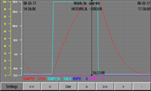
Security
Multi level security of guest, user, admin and factory level users with individual password protection All settings can be reset to factory defaults using admin login
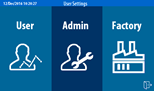
PID
6 zone based PID’s with auto recall of PID based on type of program, segment and zone can be set. Each of these PID’s can be set by using the auto tune feature or manually based on user’s requirements.
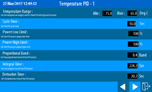
Process Mimic
Graphical representation of the working of the chamber, with live status of all the components, including the current temperature/humidity process values, compressor suction/discharge pressures and return gas temperature
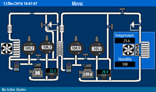
Power Resumption Modes
In case of a power failure, option of conditional restart based on temperature/time or continuous
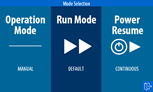
Diagnostics
Event viewer will display a log of all errors/actions with a date and time stamp PLC inputs and outputs status will be indicated
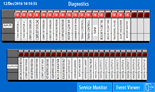
Service Monitor
Log of critical components life cycle with a predefined life cycle time and elapsed time in hours
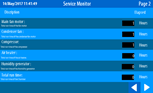
Delay Start
Real time clock based, delayed start function
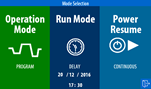