Water Spray Chamber
The water spray chamber is commonly used for conducting whole-body testing of assembled vehicles under various rain test procedures. The shed features interconnected arrays of pipes to create zones that ensure uniform spraying according to the JSS 55555 test standard. Water flows through the nozzles at a rate of up to 288 cubic meters per hour. The chamber's water collection system includes a central grating with sufficient slope to collect sprayed water during operation and circulate it back to the water reservoir for a closed-loop circulation.
The water spray chamber is commonly used for conducting whole-body testing of assembled vehicles under various rain test procedures. The shed features interconnected arrays of pipes to create zones that ensure uniform spraying according to the JSS 55555 test standard. Water flows through the nozzles at a rate of up to 288 cubic meters per hour. The chamber's water collection system includes a central grating with sufficient slope to collect sprayed water during operation and circulate it back to the water reservoir for a closed-loop circulation.
The Drive-In Rain Test Chamber is commonly used to perform whole-body testing of assembled vehicles under various rain test procedures. This helps in studying and estimating structural degradation and damage caused by rainwater. The chamber features twin shower areas with volumes of 1.1 million litres and 0.35 million litres, enclosed in a shed. Arrays of interconnected pipes form zones to ensure uniform spraying as per the JSS 55555 test standard. Water is sprayed through nozzles at a flow rate of up to 288 cubic meters per hour. The test chamber's water collection system includes a central grating with sufficient slope to collect sprayed water during operation, which is then circulated back to the water reservoir to ensure a closed-loop circulation system.
The Driving Rain Test facility is divided into multiple zones, with the operation of these zones meeting the requirements of JSS-55555. There are four zones (each 5 meters wide) for "Shower No.1" and two zones (each 5 meters wide) for "Shower No.2". A SCADA-based report generation and monitoring system is provided to track water flow rate, water pressure, and duration in graphical and tabular formats.
Got Technical Question!
Description | Shower Area 1 | Shower Area 2 | ||||||||
Workspace Dimensions - WxDxH | ||||||||||
mm | 20000 | x | 7000 | x | 8000 | 10000 | x | 7000 | x | 5000 |
In | 787 | x | 276 | x | 315 | 394 | x | 276 | x | 197 |
Volume | ||||||||||
Ltr | 1120000 | 350000 | ||||||||
Cuft | 39576 | 12367 | ||||||||
Number of Zones | 4 nos at a distance of 5m | 2 nos at a distance of 5m | ||||||||
Water flow rate/nozzle | 450 LPH +/- 45L/Nozzle | 450 LPH +/- 45L/Nozzle | ||||||||
Number of nozzles | 300 | 300 | ||||||||
Water pressure | 200 Kpa +/- 20 Kpa | 200 Kpa +/- 20 Kpa |
Ethernet
Ethernet capability to remotely monitor and control the chamber.
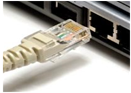
USB
USB Type-A host port to connect a keyboard or mouse or download CSV data via pen drive [max 2GB] USB Type-B data port for connection to PC for software upgrade and access memory card storage
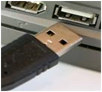
Web Server
Built-in web server allows remote view or control from any internet connected PC, tablet or smart phone
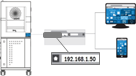
NI Lab view
The communication which used is MODBUS RTU protocol, which is an international standard for communication in process instrumentation and automation. Necessary changes to be made in the user’s software to communicate this in MODBUS RTU universal protocol. This feature can be used manual mode only.
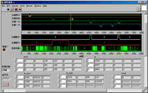
Hardware
Enhanced with modular controller integrating multi-zone PID control and data acquisition. SIMATIC programmable logic controller. Touch screen controller, PLC and other controller components are of a generic make with an OEM software. Free software upgrades up to one year.
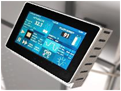
Memory
SD card of 2GB memory will store all the test program data and also the diagnostic data. This card is accessible by USB and Ethernet.
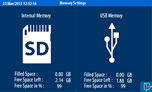
Digital Events
1 digital output for switching test specimen via potential free contacts, load max. 24 VDC, 5A
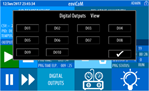
Programs
99 independent programs can be stored with name and number. Each of these programs have segments which can be looped to a previous segment and repeated up to 999 cycles, creating almost unlimited number of segments The chamber can be operated in manual mode, where the set point can directly be changed in the home screen The ramp rate can be set as a value in °C/min or ramp time Graphical representation of the temperature program The time is logged only when the set valve is within the band.
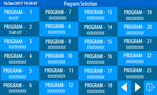
Trend Graph
Real time trend graph for temperature set value, temperature process value, humidity set value and humidity process value. Options of zoom in/out, pan and individual plot selection
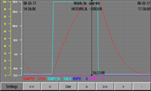
Security
Multi level security of guest, user, admin and factory level users with individual password protection All settings can be reset to factory defaults using admin login
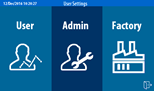
PID
6 zone based PID’s with auto recall of PID based on type of program, segment and zone can be set. Each of these PID’s can be set by using the auto tune feature or manually based on user’s requirements.
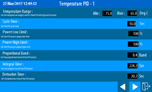
Process Mimic
Graphical representation of the working of the chamber, with live status of all the components, including the current temperature/humidity process values, compressor suction/discharge pressures and return gas temperature
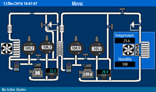
Power Resumption Modes
In case of a power failure, option of conditional restart based on temperature/time or continuous
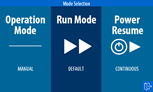
Diagnostics
Event viewer will display a log of all errors/actions with a date and time stamp PLC inputs and outputs status will be indicated
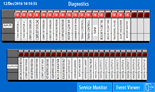
Service Monitor
Log of critical components life cycle with a predefined life cycle time and elapsed time in hours
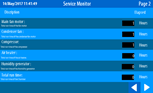
Delay Start
Real time clock based, delayed start function
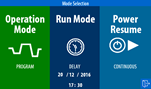